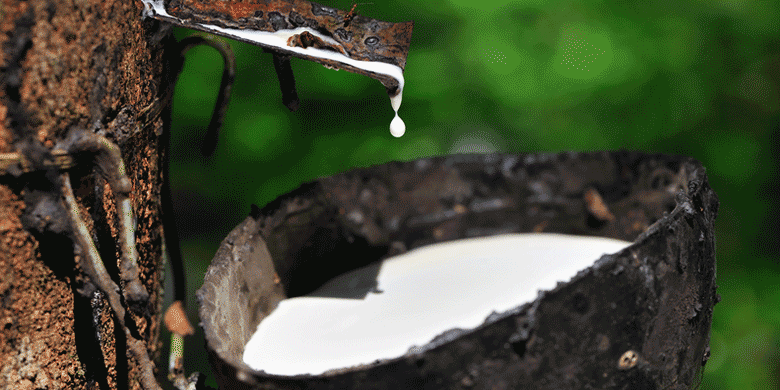
17 July, 2023
Unveiling the Magic: How Rubber Keyrings Come to Life
Rubber keyrings might seem like a simple product, but there is a lot that goes on in the background for them to be manufactured. They are commonly manufactured using a process called injection moulding. This technique allows for the production of keyrings with intricate designs, flexibility, and durability. Here is a technical analysis of the manufacturing process involved in creating rubber keyrings. I think you'll be surprised just how much effort is required to make such a small product.
Material Selection
When selecting the appropriate material for rubber keyrings, manufacturers consider factors such as the intended use, durability requirements, cost-effectiveness, and customer preferences. Both silicone and TPE offer distinct advantages and can be chosen based on the desired properties and manufacturing capabilities. Ultimately, the material selection plays a crucial role in ensuring that the rubber keyrings exhibit the desired flexibility, resilience, and resistance to wear and tear, resulting in high-quality products that meet customer expectations. Two common materials used for rubber keyring production are silicone and thermoplastic elastomer (TPE).
Due to its exceptional properties, silicone rubber is a popular choice for manufacturing rubber keyrings. It is a synthetic elastomer composed of silicon, oxygen, carbon, and hydrogen atoms. Silicone rubber exhibits excellent flexibility, allowing the keyring to bend and stretch without losing its shape. This flexibility ensures that the keyring can withstand daily use and potential stress without breaking or deforming. Silicone rubber is known for its wide temperature tolerance. It can withstand both high and low temperatures without losing its elasticity or becoming brittle. This resistance to temperature extremes makes silicone keyrings suitable for various environments and climates. Silicone rubber is resistant to many chemicals, including oils, solvents, and water. This property helps protect the keyring from damage or degradation when exposed to common substances, ensuring its longevity and performance.
TPE is another commonly used material for manufacturing rubber keyrings. It is a blend of polymers that combines the characteristics of rubber and plastic. TPE offers excellent flexibility and softness, making it ideal for creating keyrings with a comfortable feel and pleasant touch. It balances elasticity and hardness, allowing the keyring to be easily squeezed, twisted, or bent. TPE is a thermoplastic material, which means it can be melted and re-moulded multiple times without significant degradation of its properties. This property makes it suitable for various manufacturing processes, including injection moulding, which is commonly used for producing rubber keyrings. It also exhibits excellent impact resistance, which means it can withstand sudden shocks or impacts without breaking or cracking. This property ensures that the keyring can endure accidental drops or rough handling without damage.
Mould Design and Fabrication
The creation of the keyring mould is a precise and technical process that requires expertise in CAD design, CNC machining, and mould-making techniques. The accuracy and consistency of the mould directly impact the quality and consistency of the final rubber keyrings produced. By using high-quality materials and employing precise machining techniques, manufacturers can ensure that the moulds are durable, dimensionally accurate, and capable of producing keyrings that meet the desired specifications.
The first step is to create a design for the keyring mould. This involves translating the desired keyring shape and features into a 3D digital model using computer-aided design (CAD) software. The design considers factors such as the keyring's dimensions, logo or artwork placement, and additional features or textures.
The choice of material for the mould is crucial to ensure its durability, precision, and longevity. Typically, the mould is made from steel or aluminium due to their desirable properties for the manufacturing process. Steel moulds are preferred for high-volume production due to their excellent wear resistance, high-temperature resistance, and dimensional stability. Aluminium moulds, on the other hand, are lighter, more cost-effective, and suitable for lower-volume production or prototyping.
Once the material is selected, the mould is machined using precision manufacturing techniques. CNC (Computer Numerical Control) machining is commonly employed for this purpose. The CAD design is converted into instructions that guide the CNC machine to accurately cut and shape the material according to the desired specifications.
The mould is typically created in two halves that fit together to form a cavity in the shape of the desired keyring. The CNC machine precisely cuts and shapes each half of the mould, ensuring that they align perfectly when assembled. The mould cavities are designed for the desired shape, thickness, and additional features, such as raised or recessed areas.
Various surface treatments can be applied to further enhance the mould's performance and longevity. This may include polishing or texturing the mould surfaces to achieve the desired finish on the keyring. The surface treatments can also help with the release of the keyring from the mould, ensuring smooth and consistent production.
Once the mould is created, it undergoes rigorous testing and refinement processes. This involves using test samples of the selected rubber material to ensure that the mould produces keyrings with the desired shape, dimensions, and quality. Adjustments may be made to the mould design or machining process to achieve optimal results.
Injection Molding Process
The injection moulding process for rubber keyrings requires precise control of temperature, pressure, and timing to ensure consistent results. Manufacturers carefully set the parameters of the injection moulding machine to achieve the desired quality, shape, and density of the keyrings. The process is efficient and can produce a large number of keyrings in a relatively short period.
The first stage of the injection moulding process involves preparing the rubber material. The selected rubber, such as silicone or thermoplastic elastomer (TPE), is typically supplied in pellet or granule form. The rubber pellets are loaded into a hopper, which feeds the material into the injection moulding machine. Inside the injection moulding machine, a heating unit melts the rubber material. The heating unit consists of heating elements and a barrel where the rubber pellets are fed. The heat generated by the heating elements raises the temperature of the rubber to a molten state, making it fluid and ready for injection.
The machine's injection unit consists of a screw or plunger injecting molten rubber material into the mould cavity. The screw or plunger moves forward, pushing the molten rubber material under high pressure through a nozzle and into the mould cavity. The pressure ensures that the material fills the mould completely and evenly.
The injection moulding machine also includes a mould clamping mechanism, which securely holds the two halves of the mould together during the injection process. The clamping mechanism applies enough force to keep the mould closed and prevent any leakage of the molten rubber material. Once the mould clamping mechanism is engaged, the injection process begins. The screw or plunger moves forward, pushing the molten rubber material through the nozzle and into the mould cavity. The high pressure ensures that the material flows into all the mould's intricate details, replicating the keyring's desired shape and features.
After the molten rubber material is injected into the mould, it cools and solidifies. The ambient temperature facilitates the cooling process and, in some cases, additional cooling mechanisms within the injection moulding machine. As the rubber cools, it solidifies and takes on the shape of the mould cavity. The mould is opened once the rubber has solidified and the keyring has taken shape, and the ejection process begins. The mould halves separate, and ejector pins or plates help push the keyring out of the mould cavity. The keyrings are then removed from the injection moulding machine, ready for further processing and finishing.
Finishing and Quality Control
Manufacturers adhere to strict quality management systems and protocols throughout the finishing and quality control process to ensure consistency and meet customer expectations. Any keyrings that do not meet the specified standards are rejected and may undergo rework or be discarded to maintain the overall quality of the final product.
By conducting thorough finishing and quality control processes, manufacturers can ensure that the rubber keyrings are free from defects, meet the desired specifications, and are ready to be shipped to customers. These steps contribute to the overall reliability, aesthetics, and satisfaction of end-users when they use the keyrings for personal or promotional purposes.
The first step in the finishing process is trimming and deflashing the keyrings. Excess rubber or flash is carefully removed, which refers to the thin layer of material that may have seeped out of the mould during the injection process. This is typically done using specialised trimming tools like knives or cutting machines. Trimming ensures that the keyrings have clean edges and a smooth appearance.
Additional surface treatments may be applied depending on the desired finish and design of the keyrings. This can include processes such as polishing, buffing, or sanding to smoothen the surface and remove any imperfections. Surface treatment techniques help enhance the keyrings' overall aesthetic appeal and quality.
Once the keyrings are finished, they undergo a thorough inspection to ensure they meet the specified requirements and quality standards. Quality control checks are performed to assess various aspects, including dimensions, surface finish, logo or design integrity, and overall appearance. This inspection is typically carried out by trained personnel who examine each keyring individually or by using automated inspection systems.
In addition to visual inspection, keyrings may undergo functional testing to validate their performance. This can include tests such as strength and durability tests to ensure that the keyrings can withstand normal usage conditions, such as being attached to keys and subjected to bending or pulling forces. Other tests may be conducted to evaluate factors like flexibility, resistance to environmental conditions, and overall product reliability.
Once the keyrings pass the quality control checks and testing, they are ready for packaging. Keyrings are typically packed in suitable packaging materials, such as plastic bags, boxes, or blister packs, to protect them during transportation and storage. The packaging may also include proper labelling and identification of the keyrings.
In conclusion, the manufacturing process of rubber keyrings involves material selection, mould design and fabrication, material preparation, injection moulding, cooling and solidification, mould opening and ejection, finishing and quality control, optional decoration, and packaging. The use of injection moulding allows for the production of high-quality, flexible, and durable rubber keyrings with intricate designs.
The Keyrings Only Team